
How Much Is An Office Container? Complete Cost Guide for Construction Projects
How Much Is An Office Container? The Complete Cost Guide for Construction Projects
Construction project managers can expect to pay between $2,500-$35,000 for office containers, depending on size, features, and whether buying or renting. This comprehensive guide breaks down all pricing factors to help you accurately budget for your next project.
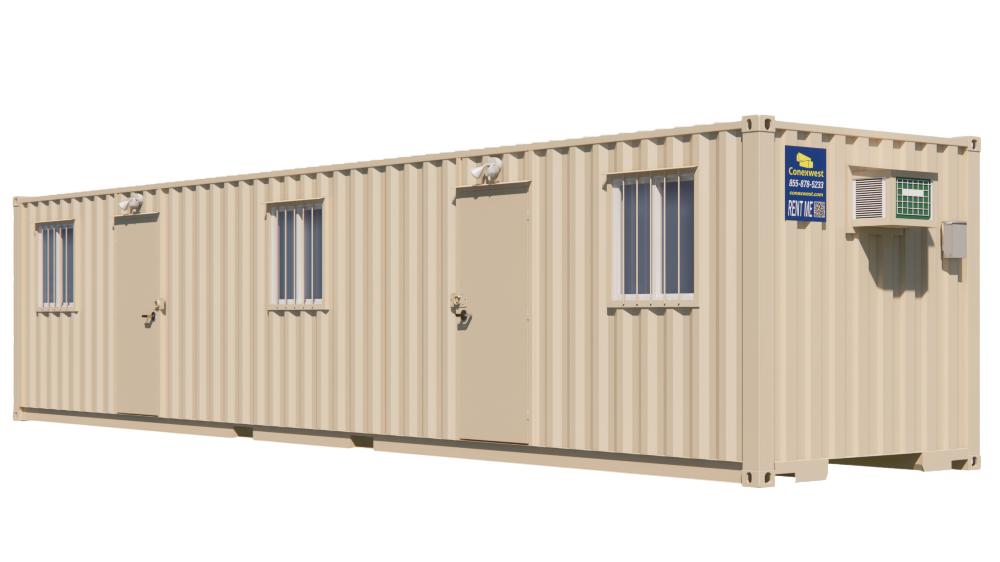
Office Container Cost Breakdown for Construction Projects
When estimating the cost of an office container for construction sites, several key factors determine the final price. Understanding these components helps project managers budget accurately and avoid unexpected expenses.
Construction companies typically recover their investment in purchased office containers within 18-24 months compared to traditional temporary office rentals, resulting in 30-40% cost savings on multi-year projects.
Size & Configuration | Purchase Price Range | Monthly Rental Range | Best For |
---|---|---|---|
8' x 20' Basic Office | $12,000 - $18,000 | $180 - $250 | Small site teams (2-3 people) |
8' x 40' Standard Office | $18,000 - $25,000 | $250 - $400 | Medium site teams (4-6 people) |
8' x 40' Deluxe Office | $25,000 - $35,000 | $400 - $600 | Project management hub (4-6 people) |
16' x 40' Double-Wide Office | $30,000 - $45,000 | $600 - $900 | Large teams or client meeting space |
Custom Multi-Container Complex | $45,000 - $100,000+ | $900 - $2,500+ | Major project headquarters |
Beyond the base price, construction companies should budget for several additional cost factors that impact the total investment in an office container solution.
One-Time Cost Factors
- Delivery fees: $200-$500 per container
- Site preparation: $500-$2,000
- Crane/lifting services (if needed): $400-$800
- Utility hookups: $500-$1,500
- Stairs/ramps/platforms: $800-$2,500
- Permits (where required): $100-$1,000
Recurring Cost Considerations
- Monthly rental fees (if applicable)
- Climate control (power costs): $50-$150/month
- Insurance: $50-$100/month
- Maintenance: $50-$200/month
- Cleaning services: $100-$300/month
- Security systems: $30-$100/month
When calculating the total cost of ownership for construction office containers, project managers should consider the project timeline. For projects lasting more than 18-24 months, purchasing often provides better return on investment than renting.
Regional Variations in Office Container Pricing
Office container costs fluctuate significantly based on geographic location. Understanding these regional factors helps construction companies develop accurate budgets for multi-region operations.
Construction companies operating in multiple regions report up to 25% price variation for identical office container specifications across different markets.
Northeast Region Pricing Factors
- Higher base pricing (10-15% above national average)
- Increased insulation requirements add $1,000-$1,500
- Snow load reinforcement costs add $800-$1,200
- Stricter permitting requirements add $300-$800
- Higher delivery costs due to urban congestion
Southwest Region Pricing Factors
- Lower base pricing (5-10% below national average)
- Enhanced cooling systems add $1,200-$2,000
- Solar options more common and cost-effective
- Dust control features add $300-$700
- Lower delivery costs in many areas
Coastal Region Pricing Factors
- Hurricane reinforcement adds $1,000-$2,500
- Corrosion-resistant materials add $700-$1,500
- Flood elevation requirements add $500-$1,200
- Higher insurance costs for coastal placement
- Special anchoring systems add $500-$1,000
Remote/Rural Area Pricing Factors
- Significantly higher delivery costs (up to $1,000+)
- Self-sufficient power options add $2,000-$5,000
- Water storage/treatment systems add $1,500-$3,000
- Satellite communication systems add $1,000-$3,000
- Enhanced security features add $800-$1,500
For construction companies operating nationally, developing region-specific budgets for office containers is essential for accurate project costing. Working with a national supplier with regional expertise can help navigate these pricing variations.
Seasonal Considerations in Office Container Costs
The construction industry experiences significant seasonal fluctuations in office container availability and pricing. Strategic timing of procurement can yield substantial cost savings.
Container office procurement during Q1 (January-March) typically results in 10-15% cost savings compared to peak season pricing during summer construction months.
Winter Season (Dec-Feb) Pricing
- Lower base prices (10-15% discount common)
- Increased likelihood of negotiation flexibility
- Faster delivery timeframes (1-2 weeks)
- Better selection of premium features
- Potential year-end inventory clearance deals
Spring Season (Mar-May) Pricing
- Gradually increasing prices
- Moderate selection availability
- Standard delivery timeframes (2-3 weeks)
- Early booking discounts still available
- Balanced negotiation leverage
Summer Season (Jun-Aug) Pricing
- Premium pricing (10-20% above baseline)
- Limited inventory of preferred configurations
- Extended delivery timeframes (3-6 weeks)
- Minimal negotiation flexibility
- Rush fees more commonly applied
Fall Season (Sep-Nov) Pricing
- Decreasing price trend
- Improving inventory selection
- Normalizing delivery timeframes
- Increasing negotiation opportunities
- End-of-fiscal-year specials
Construction companies with flexible procurement timelines can realize significant savings by securing office container solutions during off-peak seasons and storing them until needed for upcoming projects.
Featured Product: 40ft Office Container
Our 40ft Office Container provides the ideal project management headquarters for construction sites. This spacious office solution features construction-grade durability with premium office amenities.
- 320 sq ft of workspace accommodating 4-6 personnel
- Pre-installed electrical, HVAC, and communication systems
- Commercial-grade flooring designed for construction traffic
- Reinforced doors and windows with security features
- Optional interior configurations (open plan, private offices, meeting area)
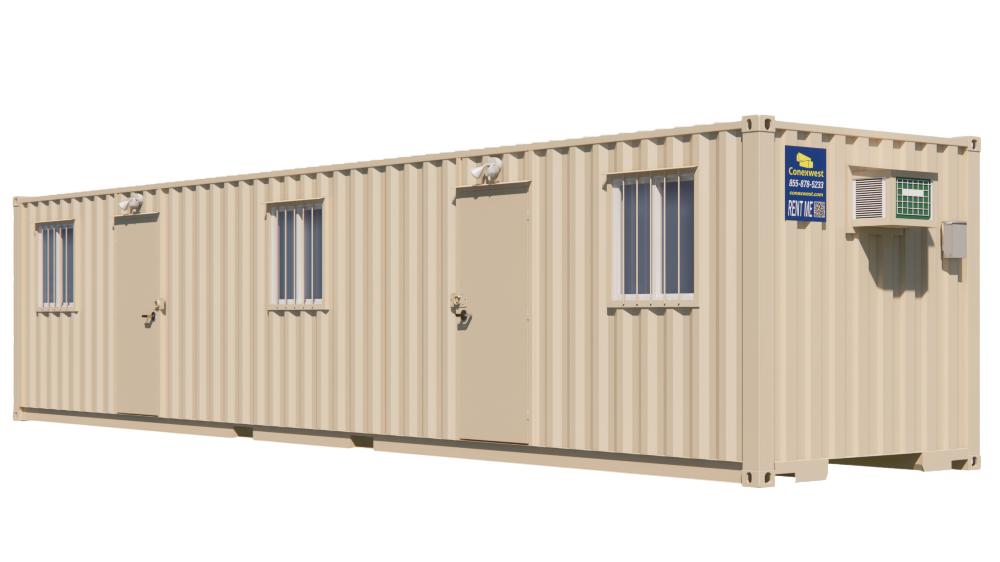
Our 40ft office containers begin at $22,000 for purchase and $350/month for rental, with customization options available to meet specific project requirements. Volume discounts available for multi-unit orders.
Featured Product: 20ft Office Container with Restroom
The 20ft Office Container offers the perfect solution for smaller construction sites where space efficiency is essential without sacrificing necessary amenities.
- 160 sq ft optimized layout with optional integrated restroom facility
- Self-contained water and waste systems (optional city connections)
- Complete electrical package with construction-grade components
- Reinforced construction for frequent relocation between sites
- Turnkey solution requiring minimal site preparation
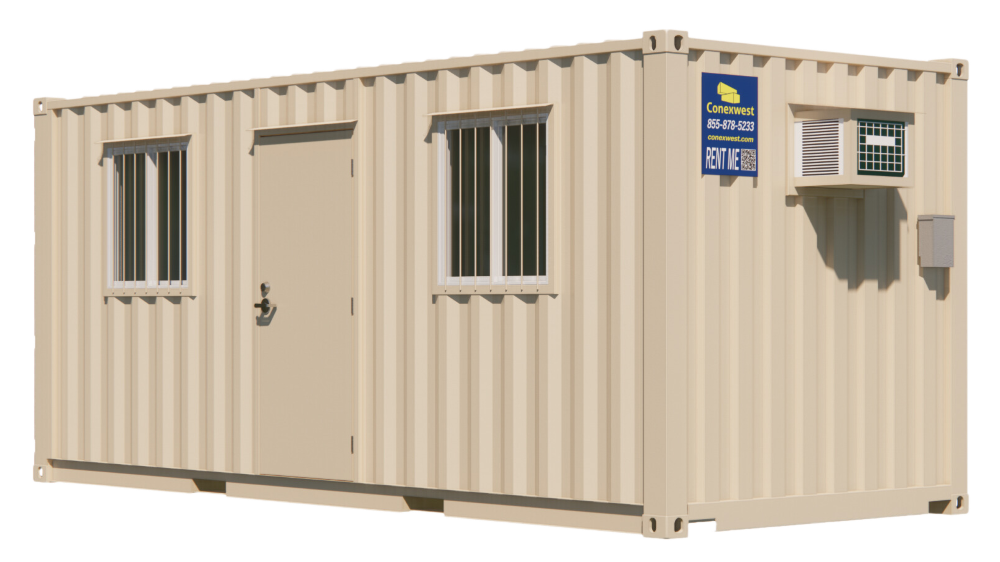
Starting at $16,500 for purchase and $275/month for rental, this solution eliminates the need for separate restroom facilities while providing a professional workspace for site management.
Cost Comparison: Office Containers vs. Traditional Construction Trailers
Construction project managers must often choose between container offices and traditional construction trailers. Understanding the complete cost implications of each option reveals why containers are increasingly the preferred choice.
While initial pricing may appear similar, construction companies report 30-40% lower total cost of ownership with container offices compared to traditional trailers over a 3-5 year period.
Cost Factor | Office Container | Traditional Construction Trailer |
---|---|---|
Initial Purchase (20ft unit) | $15,000 - $20,000 | $15,000 - $25,000 |
Monthly Rental | $200 - $350 | $250 - $450 |
Transportation Costs | $200 - $500 per move | $500 - $1,200 per move |
Setup/Teardown | $300 - $600 | $800 - $1,500 |
Annual Maintenance | $500 - $1,000 | $1,200 - $2,500 |
Energy Efficiency | 15-30% more efficient | Standard efficiency |
Resale Value (after 5 years) | 50-60% of purchase price | 20-30% of purchase price |
Security Features | Superior (steel construction) | Standard (wood construction) |
Beyond direct cost comparisons, container offices offer construction companies additional value through faster deployment, enhanced security, and significantly higher resale value.
Step-by-Step Guide to Budgeting for a Construction Office Container
Accurate budgeting for office containers requires a systematic approach. This process ensures all costs are captured and contingencies are established for construction project planning.
Construction project managers report that following a structured budgeting process for office containers prevents an average of $2,500 in unexpected costs per unit.
Determine Specific Requirements
Assess team size, required amenities, project duration, and site constraints. Document specific needs such as number of workstations, meeting space requirements, climate control specifications, and communication needs.
Tools needed: Requirements checklist, team input survey, site assessment report
Calculate Space Requirements
For construction management, allow 50-75 sq ft per person. Determine whether a 20ft unit (160 sq ft), 40ft unit (320 sq ft), or custom configuration is appropriate based on team size and functions.
Tools needed: Space planning calculator, organizational chart
Develop Base Unit Budget
Determine whether purchase or rental makes more sense based on project timeline and future needs. Budget for the base unit cost using current market rates for the selected configuration.
Tools needed: ROI calculator, vendor quotes, market price analysis
Add Site Preparation Costs
Budget for foundation requirements, access preparation, and utility connections. Include permitting costs where applicable and any required site modifications.
Tools needed: Site evaluation report, local contractor quotes
Include Transportation and Installation
Budget for delivery, crane/lifting services (if needed), and final positioning. Factor in access challenges that may increase costs like limited site access or difficult terrain.
Tools needed: Transportation quotes, site logistics plan
Calculate Operational Costs
Budget for monthly utilities, maintenance, insurance, security, and other recurring expenses. Create a monthly operational budget for the duration of the project.
Tools needed: Utility rate calculators, maintenance schedules, insurance quotes
Add Customization and Outfitting
Budget for office furniture, equipment, network setup, security systems, and any required branding or customization.
Tools needed: Office outfitting checklist, vendor quotes
Include Contingency
Add 10-15% contingency to cover unexpected costs, price increases, or change orders. This buffer prevents budget overruns when unforeseen expenses arise.
Tools needed: Risk assessment worksheet, historical cost variance data
Calculate Total Cost of Ownership
Combine all costs and project over the entire project timeline. Compare different options (purchase vs. rent, different sizes, etc.) based on total cost of ownership rather than just initial price.
Tools needed: TCO calculator, project timeline
This structured budgeting approach ensures construction companies capture all potential expenses when planning for office container procurement, preventing mid-project budget surprises.
Environmental Impact and Cost: Sustainable Office Container Options
Increasingly, construction companies must balance environmental responsibilities with cost considerations. Understanding the financial implications of sustainable office container options helps inform these decisions.
Energy-efficient container offices typically command a 10-15% premium but deliver 20-30% operational cost savings over a 5-year period while reducing carbon footprint by up to 40%.
Standard Container Environmental Costs
- Average energy consumption: 30-40 kWh/day
- Typical carbon footprint: 5-7 tons CO2/year
- Water usage (with restroom): 400-500 gallons/week
- Limited material recyclability at end-of-life
- Standard waste management requirements
Eco-Friendly Container Investment Premium
- Enhanced insulation: +$800-$1,500
- Energy-efficient HVAC: +$1,200-$2,000
- LED lighting systems: +$300-$600
- Low-VOC materials: +$500-$900
- Solar power options: +$3,000-$8,000
Eco-Friendly Container Cost Savings
- Energy cost reduction: 20-30%
- Extended lifespan: +2-3 years
- Higher resale value: +15-20%
- Potential tax incentives: varies by location
- Improved worker productivity: 5-8%
Green Certification Cost Considerations
- LEED-compliant container premium: +15-25%
- Energy Star certification process: $500-$1,500
- Documentation requirements: 20-30 labor hours
- Ongoing compliance monitoring: $300-$800/year
- Marketing value of certification: significant
For construction companies emphasizing sustainability, the additional investment in eco-friendly office containers typically pays for itself through operational savings, enhanced corporate image, and potential project qualification advantages.
Frequently Asked Questions About Office Container Costs
- What's the price difference between buying and renting an office container?
For a standard 20ft office container in the construction industry, purchase prices typically range from $15,000-$25,000 while monthly rentals range from $200-$350. The breakeven point between renting and buying usually occurs between 18-24 months. For projects lasting longer than two years, purchasing is typically more economical. However, rental eliminates long-term maintenance responsibilities and provides flexibility for changing project needs. Many suppliers also offer rent-to-own options that convert a portion of rental payments toward eventual purchase.
- What hidden costs should construction companies watch for when budgeting for office containers?
Common hidden costs include: delivery fees ($200-$500), site preparation ($500-$2,000), permit fees ($100-$1,000 depending on jurisdiction), utility connection costs ($500-$1,500), accessibility requirements like stairs and ramps ($800-$2,500), security setup ($300-$1,000), network/communication infrastructure ($500-$2,000), insurance premium increases ($50-$100/month), and decommissioning/removal costs ($200-$500). Additionally, customizations can significantly impact price, often adding 20-40% to base costs. Always request a detailed quote that includes all potential charges.
- How much do custom modifications add to the price of a construction office container?
Custom modifications can significantly impact office container pricing for construction sites. Basic modifications like additional windows ($300-$600 each), extra doors ($600-$1,200 each), or interior partitions ($1,000-$3,000) add incremental costs. More substantial modifications like restrooms ($3,000-$6,000), kitchenettes ($1,500-$3,000), enhanced HVAC systems ($2,000-$4,000), or specialized electrical configurations ($1,000-$3,000) can increase the base price by 25-50%. Highly customized containers with premium finishes, specialized security, or multi-room configurations can double the base price or more.
- What factors most significantly impact office container costs for construction sites?
The most significant cost factors for construction office containers are: size/square footage (20ft vs. 40ft can double the price), new vs. used condition (used units typically cost 30-50% less), interior finish quality (basic vs. premium can vary by $5,000-$10,000), climate control capabilities (basic vs. advanced systems vary by $2,000-$4,000), delivery location (remote sites can increase delivery costs by 50-100%), site accessibility (difficult access requiring specialized equipment can add $500-$1,500), and market timing (peak construction season prices can be 10-20% higher than off-season). Project duration also significantly impacts total cost when comparing rental vs. purchase options.
- How do financing options affect the total cost of an office container?
Financing typically increases the total cost of office containers by 10-25% depending on terms and credit rating. Most suppliers offer 2-5 year financing plans with interest rates ranging from 5-12%. For a $20,000 container financed over 36 months at 8% interest, the total cost increases by approximately $2,500. However, financing provides immediate tax advantages through depreciation while preserving capital for other project needs. Many construction companies find that financing at current interest rates yields better ROI than using cash, especially when the container is generating project efficiencies. Lease-to-own programs typically cost 5-10% more than direct financing but offer more flexibility.
- What's the typical ROI calculation for an office container on a construction project?
Construction companies typically calculate ROI for office containers by comparing them to alternatives (traditional trailers, off-site offices, or rental space) and factoring in productivity improvements. A standard calculation includes: cost savings from elimination of off-site space ($1,000-$3,000/month), reduced travel time for personnel (30-60 minutes per person daily), improved on-site supervision (typically reducing rework by 5-10%), enhanced document control, and improved client communication. For a typical medium-sized project, companies report that on-site office containers provide ROI of 150-200% over the project duration when all factors are considered, with the container often retaining 50-60% of its value for future projects.
- How much should we budget for site preparation for an office container?
Site preparation costs for construction office containers vary based on existing conditions but typically range from $500-$2,000. Basic preparation on relatively level ground with good access might only require gravel leveling ($300-$600). More complex sites may need concrete footings or piers ($800-$1,500), drainage improvements ($400-$800), access path creation ($300-$700), or utility trenching ($500-$1,000). Remote or challenging sites with poor soil conditions may require engineering analysis ($500-$1,000) and enhanced foundation systems ($1,500-$3,000). Most construction companies find it economical to use existing site equipment and personnel for basic preparation, potentially reducing these costs by 30-50%.
- What's the typical depreciation schedule and resale value for an office container?
For tax purposes, office containers used in construction are typically depreciated over 7 years using MACRS, though some components may qualify for 5-year depreciation. Well-maintained office containers retain approximately 60-70% of their value after 3 years, 40-50% after 5 years, and 30-40% after 7 years. Premium containers with higher-quality finishes and regular maintenance tend to hold value better than basic models. The resale market for construction office containers remains strong, with units in good condition typically selling within 30-60 days when properly priced. Many construction companies establish container rotation programs, selling units after 5-7 years to optimize the balance between depreciation benefits and maintenance costs.
- How does container office cost compare to traditional construction for permanent site offices?
For permanent site offices, container solutions typically cost 30-40% less than traditional construction while being completed 70-80% faster. A 1,000 sq ft permanent office built with traditional methods costs approximately $150-$200 per square foot ($150,000-$200,000 total) and takes 4-6 months to complete. An equivalent container office complex costs approximately $100-$130 per square foot ($100,000-$130,000) and can be operational in 3-6 weeks. The accelerated timeline alone provides significant value through earlier operational capability. While traditional construction offers more design flexibility, modern container office complexes offer comparable aesthetics with superior durability and future flexibility, including potential relocation capabilities that traditional construction cannot match.
- What ongoing maintenance costs should be budgeted for an office container?
Annual maintenance costs for construction office containers typically range from 3-5% of the initial purchase price. For a $20,000 office container, annual maintenance budgets should be $600-$1,000. Key maintenance expenses include: HVAC service ($200-$400 annually), exterior painting/sealing every 3-5 years ($800-$1,500), door/window hardware maintenance ($100-$300 annually), roof inspection and sealing ($200-$500 annually), flooring repair/replacement every 5-7 years ($1,000-$3,000), and electrical system inspections ($150-$300 annually). Harsh environments like coastal or extreme temperature regions may increase these costs by 20-30%. Preventative maintenance programs typically reduce overall costs by 15-25% compared to reactive maintenance approaches.
Conclusion: Maximizing Value When Purchasing Construction Office Containers
Making a smart investment in a construction office container requires balancing initial costs against long-term value. The right approach can significantly reduce total cost of ownership while enhancing project efficiency.
Construction managers report that strategic office container procurement typically yields 15-20% cost savings compared to reactive purchasing while improving project efficiency by 7-12%.
Cost-Saving Strategies
- Purchase during off-peak seasons (Q4-Q1)
- Consider certified pre-owned units (30-50% savings)
- Opt for standardized rather than fully custom units
- Bundle multiple unit purchases for volume discounts
- Explore rent-to-own programs for uncertain timelines
Value-Maximizing Features
- Prioritize durability over cosmetic features
- Invest in superior insulation and climate control
- Choose flexible interior configurations
- Ensure robust electrical systems with expansion capacity
- Select units with proven resale or redeployment potential
For construction companies looking to optimize their investment in office container solutions, ConexWest provides industry-leading expertise in matching the right container configuration to specific project requirements and budget parameters.
Our construction industry specialists can help you navigate all aspects of office container procurement, from initial budgeting through delivery and setup. Whether you're seeking a basic single-unit solution or planning a comprehensive multi-container project headquarters, our team can develop a customized solution that maximizes value while meeting your specific operational requirements.