How To Seal Shipping Container Floors
Get a quoteGuide to Sealing Shipping Container Floors
Key Takeaways
- Sealing shipping container floors prevents moisture damage and extends the life of the container.
- Choosing the right sealant is essential for effective protection against environmental elements.
- A well-sealed floor reduces health risks associated with chemical exposure from treated wood.
- Regular maintenance and resealing can save money in the long run by avoiding costly repairs.
- Conexwest’s reliable shipping container fabrication service provides safer and more effective results than sealing the container on your own.
Why Seal Shipping Container Floors
1. Protection Against Chemical Exposure
Shipping container floors, often made of plywood or bamboo, are treated with pesticides to prevent insect infestations during transport. While these treatments are effective, they can release harmful fumes over time, especially in enclosed spaces.
Sealing the floors with a non-breathable material, such as epoxy, can trap these chemicals and mitigate health risks.
2. Enhancing Durability and Longevity
- Physical Protection: Sealing the floor with an epoxy coating or other durable materials helps protect against physical damage from heavy loads and environmental factors.
- Water Resistance: Many sealing options provide water resistance to prevent moisture damage that can lead to mold growth or deterioration of the underlying materials.
3. Maintenance and Cleanliness
Sealed floors are easier to clean and maintain. For instance, vinyl flooring or epoxy coatings can be wiped down or hosed off without damaging the surface.
4. Cost-Effectiveness
By sealing the floor initially, you can avoid costly repairs down the line due to damage from pests or moisture.
Conexwest, a leader in shipping and storage solutions based in Northern California, offers new, used, and refurbished containers from 10ft to 45ft, with fast delivery within 3–7 days and container fabrication options like adding shelves and locks. We serve over 10,000 customers nationwide, including prestigious clients like the U.S. Navy and Google. As an ISO 9001 and AWS-certified company, we ensure top quality and competitive pricing. |
Step-by-Step Process To Seal The Floor
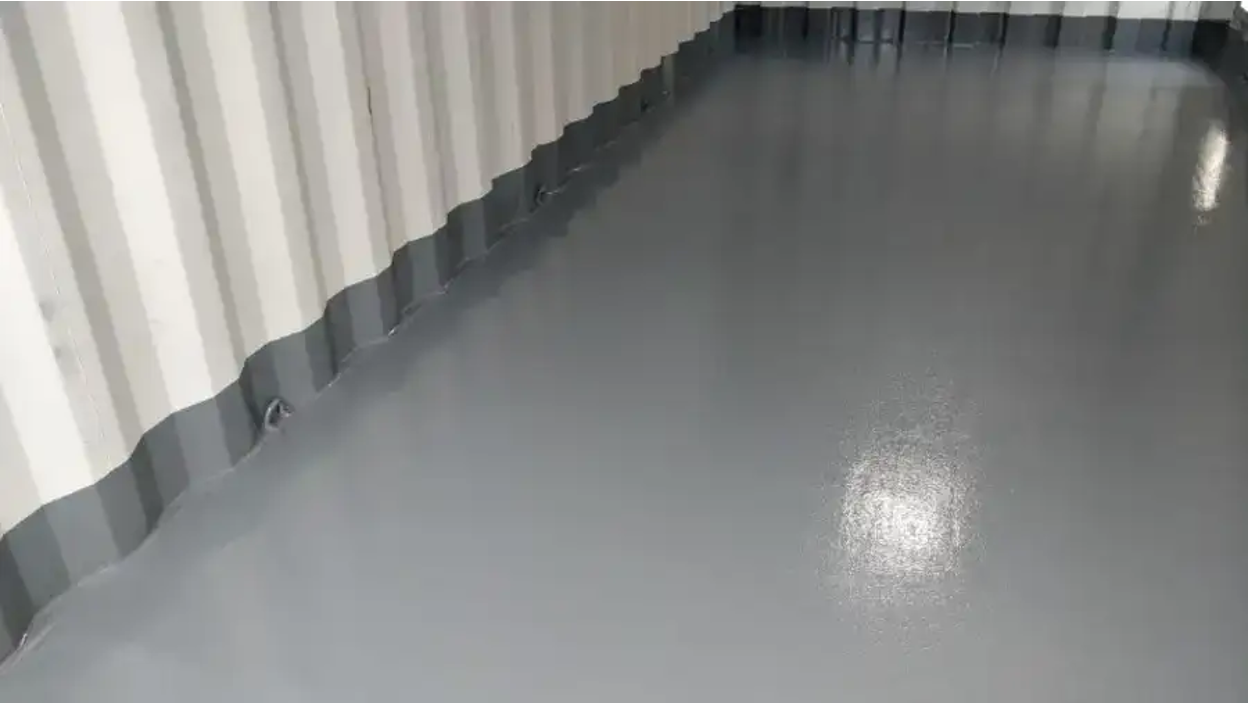
Epoxy sealant on the floor looks elegant as well!
1. Inspect the Floor
- Identify Damage: Check for any gaps, holes, or damage in the existing flooring. Look for signs of moisture or pest infestation.
- Assess Chemical Treatment: Review the container's CSC plate for information on any chemicals used in the flooring treatment.
2. Prepare the Area
- Clean the Surface: Remove debris, dust, and any loose material from the floor using a broom or vacuum. For stubborn stains, consider using a mild detergent and water.
- Dry the Floor: The floor should be completely dry before proceeding with sealing.
3. Repair Any Damage
- Dowel Repairs: For small holes (up to 22mm), insert hardwood dowels secured with adhesive, then trim and smooth them to restore surface integrity.
- Replace Damaged Sections: If larger sections are damaged, remove them carefully and replace them with new plywood or other suitable materials. Secure with screws and apply sealant to joints.
4. Apply Sealant
- Choose a Sealant: Select an appropriate sealant such as epoxy or polyurethane that is compatible with the flooring material. Epoxy is particularly effective as it creates a strong barrier against moisture and chemicals.
- Application Process:
- Use a paint roller or brush to apply an even coat of sealant across the entire floor surface.
- Pay special attention to seams and joints. They should be thoroughly covered to prevent water ingress.
- For best results, apply multiple coats as recommended by the manufacturer, allowing adequate drying time between each coat.
5. Finishing Touches
- Check for Gaps: After sealing, inspect again for any missed gaps or areas needing additional sealant.
- Final Inspection: Make sure that the sealed surface is smooth and uniform. This will help in maintaining cleanliness and ease of use.
6. Allow to Cure
- Let the sealant cure completely before placing any items inside the container or subjecting it to foot traffic.
7. Regular Maintenance
- Periodically check the sealed areas for wear and tear. Reapply sealant as necessary to maintain protection against moisture and pests.
Common Mistakes To Avoid When Sealing The Floor
- Ignoring Repairs: Not addressing existing damage, such as rot or holes, prior to sealing can compromise the seal's effectiveness. Always repair any damage first.
- Using Incompatible Sealants: Choosing a sealant that is not suitable for the flooring material can result in peeling or ineffective sealing. Select a sealant specifically designed for your flooring type.
- Applying Sealant Too Thickly: Over-applying sealant can cause it to crack or peel as it cures. It’s better to apply multiple thin coats rather than one thick layer.
- Sealing in Poor Weather Conditions: Applying sealant during humid or rainy weather can prevent proper curing and adhesion. Choose dry weather for application.
- Rushing the Curing Process: Not allowing sufficient time for the sealant to cure can lead to premature failure. Follow manufacturer instructions for drying times.
How Conexwest Can Help You Seal Shipping Container Floor

With Conexwest’s expertise, your sealant project will be completed to perfection.
If you want to seal the floor of your shipping container, we at Conexwest are here to provide you with a comprehensive and customized solution. Here’s how:
1. Expert Guidance
Our team of experts is ready to guide you through every step so you make informed decisions about the best sealant options for your container type and intended use.
2. Professional Services
Our skilled technicians have experience in sealing container floors and will make sure that everything is applied correctly for optimal performance.
3. Maintenance Support
After sealing your container floor, we don’t just leave you hanging. We provide ongoing support and maintenance tips to help you keep your container in top condition. Regular inspections and maintenance can prolong the life of your sealed floor, and we’re here to assist you with that.
Frequently Asked Questions (FAQs)
- What types of sealants are best for shipping container floors?
The best sealants for shipping container floors are epoxy or polyurethane-based. Epoxy sealants are durable and resistant to water, which makes them ideal for containers exposed to harsh weather. Polyurethane sealants provide flexibility and are suitable for environments with temperature fluctuations.
- How often should I reseal the floor?
It's generally recommended to reseal the container floor every 3 to 5 years, depending on usage and environmental conditions. Regular inspections can help you determine if resealing is necessary sooner. Look for signs of wear, such as peeling or cracking, which indicate that the sealant is losing its effectiveness.
- Can I use regular paint as a sealant?
Regular paint is not a suitable substitute for sealant. While it might provide some protection, it lacks the durability and moisture resistance needed for effective sealing.
- How long does it take for sealant to cure?
Curing times can vary based on the type of sealant used, but typically, it can take anywhere from a few hours to several days for complete curing. Refer to the manufacturer's instructions for guidance.
- What types of modifications can Conexwest make to shipping containers?
We provide a wide range of modifications, including adding windows, vents, partitions, shelving systems, and customized paint. Our team can help you customize your container to suit various applications - from storage units to mobile offices.