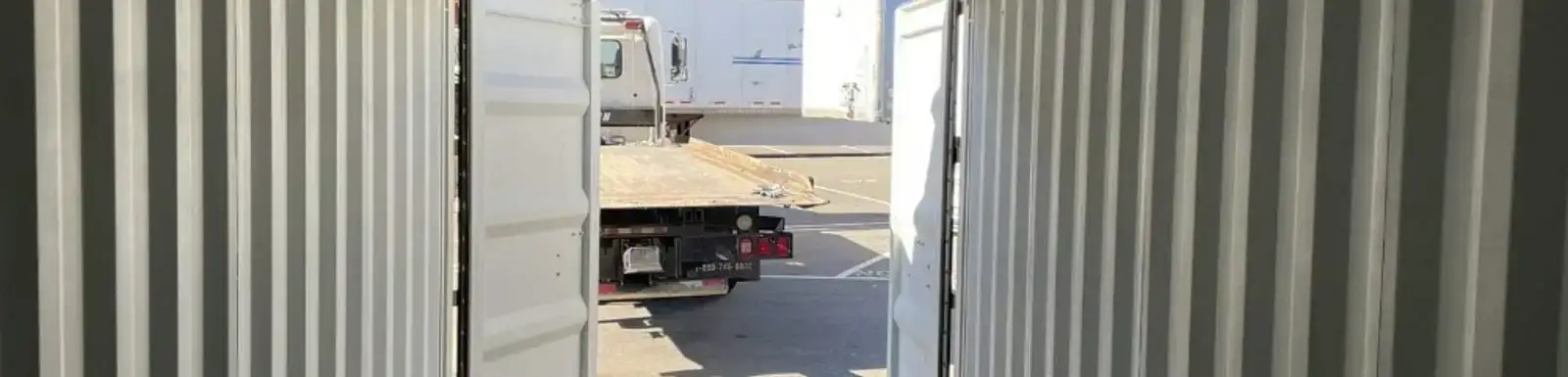
Shipping Container Modifications: The Complete Guide
Shipping Container Modifications: The Complete Guide
Shipping container modifications have revolutionized how businesses and individuals approach construction projects. This comprehensive guide explores the full spectrum of container modifications, from basic alterations to complex custom builds, helping you understand the possibilities, processes, and practical considerations.
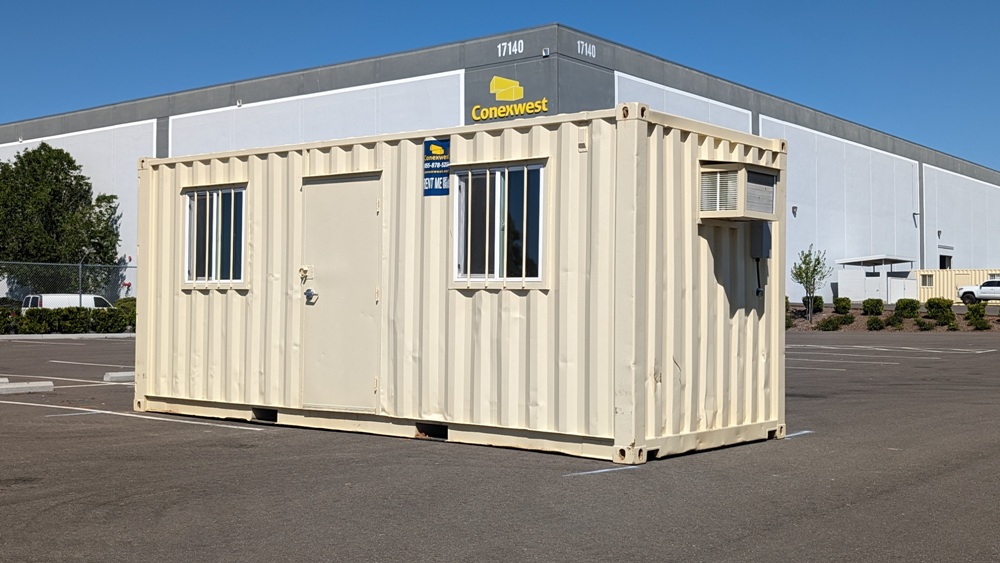
Understanding Container Modification Fundamentals
Shipping containers are designed as standardized, durable steel boxes for global transportation, but their inherent strength and modular nature make them ideal for structural modifications. Understanding the fundamental aspects of container construction is essential before embarking on any modification project.
A properly modified shipping container can retain over 90% of its original structural integrity while being transformed into virtually any functional space imaginable.
Container Modification Advantages
- Built-in structural integrity
- Weatherproof and durable design
- Standardized dimensions for predictable planning
- Mobility and relocatability
- Rapid deployment compared to traditional construction
- Sustainable repurposing of existing materials
Container Types for Modification
- Standard containers (8' × 8'6" × 20'/40')
- High cube containers (additional foot of height)
- Open top containers for unique vertical projects
- Flat rack containers for custom floor plans
- Refrigerated containers for climate-sensitive applications
- One-trip containers (newest condition)
Before selecting a container for modification, consider the container condition, as it significantly impacts the modification process. Containers are typically categorized as:
Container Grade | Characteristics | Best Applications |
---|---|---|
One-Trip (New) | Minimal wear, no rust, pristine condition | Living spaces, offices, retail, food service |
Cargo Worthy | Moderate wear, fully functional, may have cosmetic issues | Workshops, storage, industrial applications |
Wind & Water Tight | More significant wear, but still sealed against elements | Basic storage, temporary structures, budget projects |
Featured Product: 20ft One-Trip Container
The ideal foundation for high-end modifications, one-trip 20ft containers offer the cleanest starting point for your project with:
- Pristine steel surfaces ideal for custom finishes
- No prior cargo contamination
- Manufacturer warranties still intact
- Perfect dimensions for small businesses and compact applications
- Excellent structural integrity for complex modifications
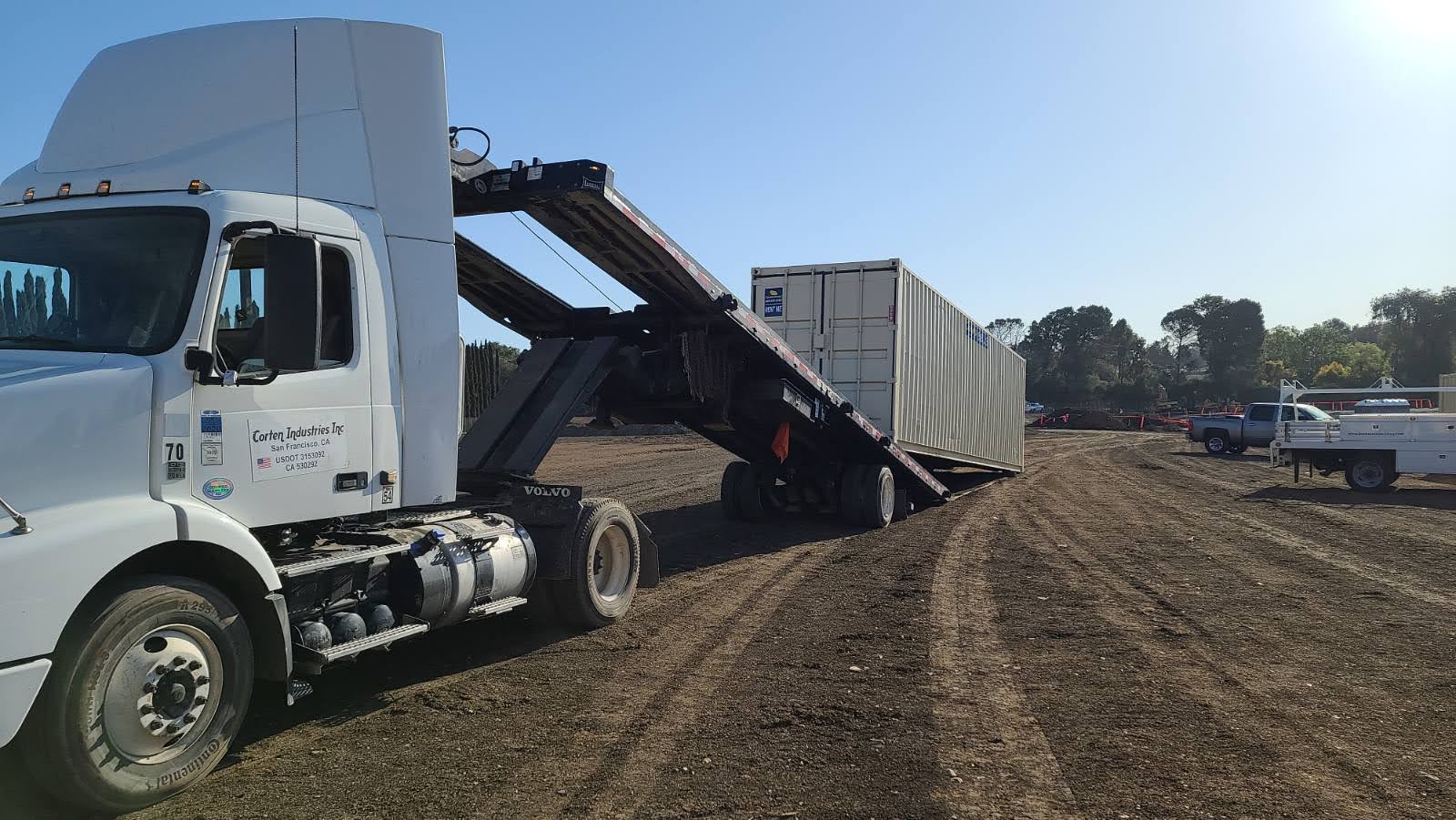
Common Structural Modifications
Structural modifications form the foundation of container conversion projects, allowing for customized spaces while maintaining safety standards. Professional modification services ensure these changes meet building codes and structural requirements.
When properly reinforced, a standard shipping container can have up to 70% of its wall area removed for windows, doors, and interconnections without compromising structural integrity.
Door and Window Installations
- Personnel doors with commercial-grade hardware
- Roll-up doors for equipment access
- Dutch doors for service windows
- Fixed windows with security features
- Sliding glass doors for modern aesthetics
- Custom window configurations for unique designs
Wall Modifications
- Wall removal for open floor plans
- Structural reinforcement for stability
- Container combining for larger spaces
- Side panel replacements
- Load-bearing reinforcements
- Custom wall cutouts with header supports
When planning door and window placements, consider both functional needs and structural requirements. Strategic positioning can maximize natural light while minimizing the need for additional reinforcement.
Featured Product: Personnel Door with Window
A popular modification option, commercial-grade personnel doors provide secure access while adding natural light with integrated windows:
- Commercial-grade steel construction
- Weather-sealed for climate control
- High-security locking mechanisms
- Optional window for natural light
- Customizable placement on any container wall
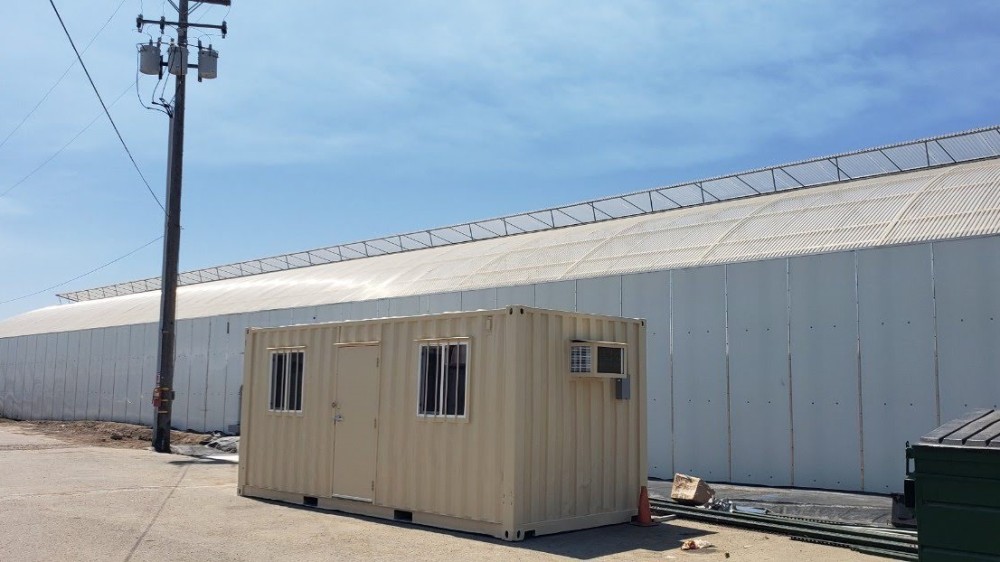
Electrical and Climate Control Systems
Modern container modifications typically require electrical systems and climate control to create comfortable, functional spaces. Professional container specialists can integrate these systems safely and efficiently.
Electrical System Components
- Service panels (100-200 amp)
- Interior and exterior lighting
- Commercial-grade wiring
- GFCI protection for safety
- Multiple outlet configurations
- Data and communications wiring
Climate Control Options
- HVAC systems (wall-mounted mini-splits)
- Through-wall air conditioning units
- Electric heating systems
- Insulation packages (spray foam, panel, reflective)
- Ventilation systems with air exchange
- Smart climate control technologies
Proper insulation is critical for container modifications, as steel conducts heat 1,000 times faster than wood, making uninsulated containers unsuitable for human occupancy in most climates.
The R-value (thermal resistance) of insulation in container projects is particularly important. While traditional construction typically aims for R-13 to R-19 in walls, container projects often require higher values to compensate for steel's thermal conductivity.
Featured Product: HVAC Package
Integrated climate control systems transform containers into year-round comfortable spaces with:
- Energy-efficient mini-split systems
- Heating and cooling capabilities
- Low-profile design to maximize interior space
- Programmable temperature control
- Professional installation with proper sealing
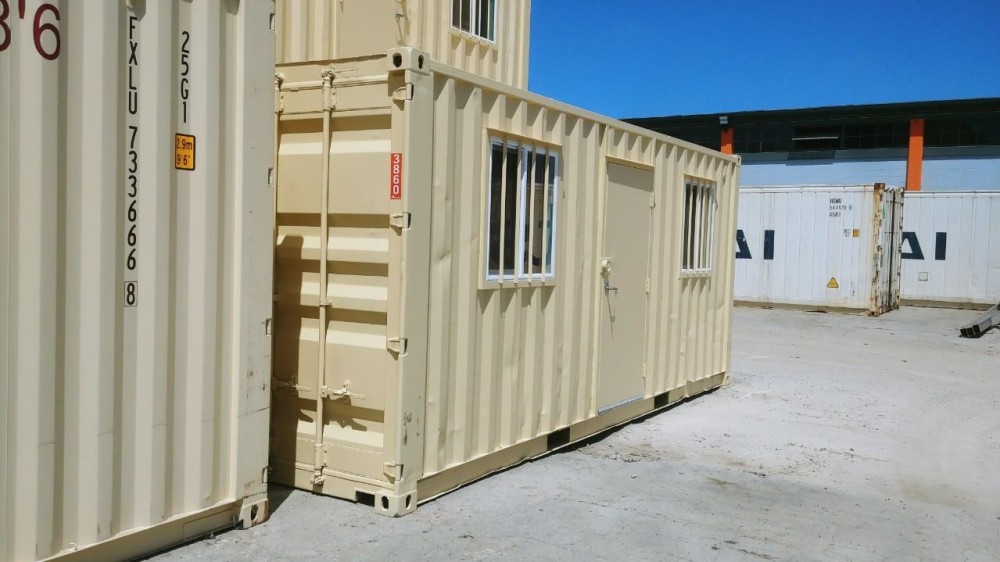
Interior Finishing Options
Interior finishes transform raw containers into comfortable, functional spaces. The right combination of materials creates environments that meet specific needs while maintaining durability and safety standards.
Flooring Systems
- Commercial-grade vinyl
- Epoxy coatings for industrial use
- Engineered hardwood for upscale applications
- Anti-fatigue flooring for workshops
- Raised access flooring for utilities
- Marine-grade plywood subflooring
Wall and Ceiling Treatments
- Fire-rated drywall systems
- FRP (fiberglass reinforced panels)
- Plywood with decorative finishes
- Steel wall liners for durability
- Acoustic treatments for sound control
- PVC wall and ceiling panels
When selecting interior finishes, consider the container's purpose, climate conditions, and maintenance requirements. Office container conversions typically feature different finishes than industrial or storage applications.
Featured Product: Premium Office Finishing Package
Transform your container into a professional business-ready office space with comprehensive finishing:
- Commercial-grade vinyl plank flooring
- Insulated walls with drywall finishing
- Suspended ceiling with LED lighting
- Climate control system integration
- Data ports and electrical outlets
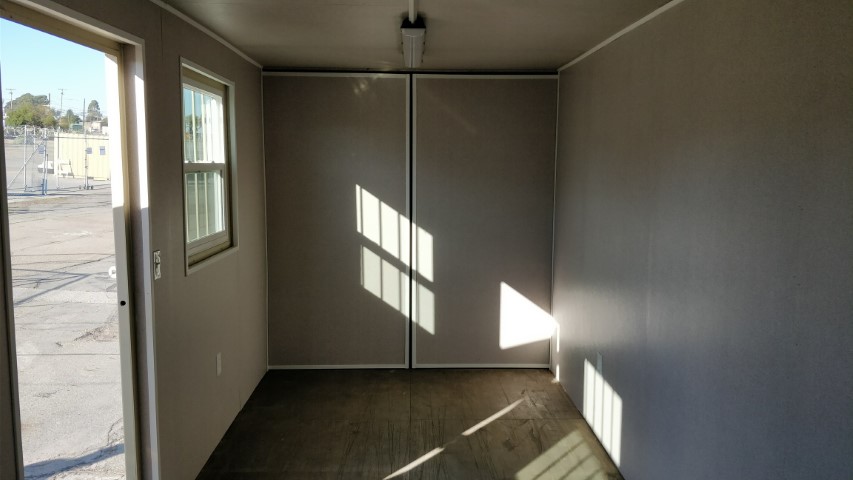
Specialized Container Applications
Container modifications have evolved to serve specialized industries with custom solutions designed for specific operational needs. These purpose-built modifications demonstrate the versatility of container architecture.
The standardized dimensions of shipping containers allow for consistent, replicable modifications that can be deployed globally with minimal site preparation, making them ideal for scalable business solutions.
Common Specialized Applications
- Mobile offices and workspaces
- Equipment enclosures and pump houses
- Generator housing and utility buildings
- Laboratory and testing facilities
- Retail pop-ups and food service
- Construction site facilities
Industry-Specific Considerations
- Hazardous material storage requirements
- Healthcare facility compliance standards
- Food service health code accommodations
- Technology infrastructure for data centers
- Security features for valuable inventory
- Explosion-proof requirements for industrial use
Industry-specific modifications require careful attention to regulatory compliance. Container storage solutions for specialized applications must meet industry standards while providing practical functionality.
Featured Product: Equipment Enclosure
Protect valuable equipment with specialized container enclosures designed for industrial applications:
- Weather-tight and secure housing
- Climate control for sensitive equipment
- Custom access points for maintenance
- Reinforced flooring for heavy machinery
- Integrated electrical and ventilation systems
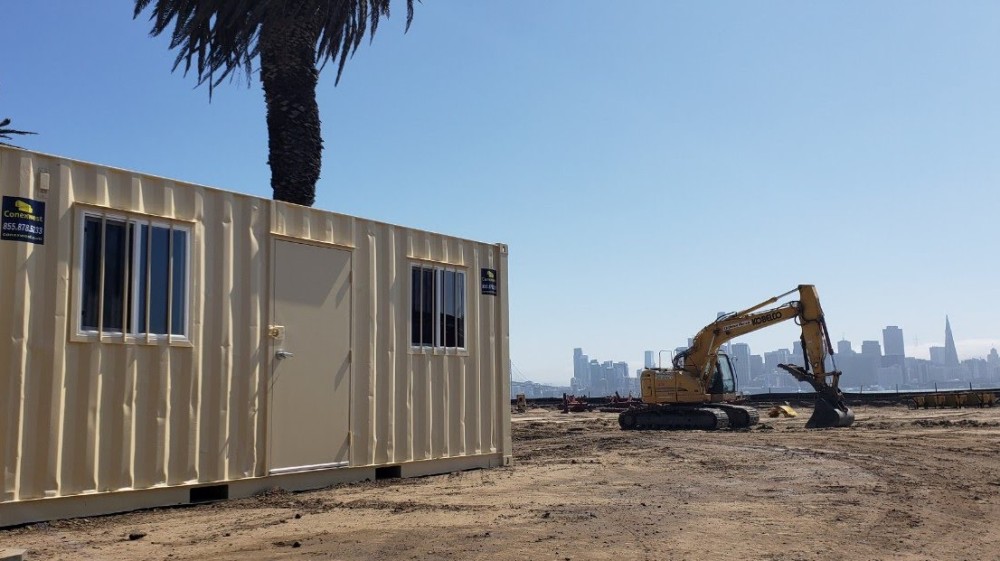
The Container Modification Process
Understanding the container modification process helps set realistic expectations for your project timeline and budget. Professional modification services follow a structured approach to ensure quality results.
Typical Modification Timeline
- Consultation and needs assessment: 1-2 weeks
- Engineering and design: 2-4 weeks
- Permitting (if required): 2-8 weeks
- Container preparation: 1 week
- Structural modifications: 1-3 weeks
- Systems installation: 1-2 weeks
- Interior finishing: 1-3 weeks
- Quality assurance and testing: 1 week
Key Modification Considerations
- Local building code compliance
- Site preparation requirements
- Foundation needs and anchoring
- Weather conditions during modification
- Access for delivery equipment
- Utility connection planning
- Future expansion possibilities
- Long-term maintenance planning
While DIY container modifications are popular online, professional modifications offer critical advantages in structural integrity, code compliance, and warranty protection that can prevent costly problems down the line.
Working with experienced container modification specialists ensures your project meets safety standards and performs as expected for years to come. Professional modifications typically include warranties and ongoing support that DIY projects cannot match.
Cost Factors for Container Modifications
Container modification costs vary widely based on several factors. Understanding these variables helps develop realistic budgets for your container project.
Modification Type | Basic Cost Range | Premium Cost Range |
---|---|---|
Personnel Door Installation | $1,200 - $2,500 | $2,500 - $4,000 |
Window Installation | $800 - $1,500 per window | $1,500 - $3,000 per window |
HVAC System | $3,500 - $5,000 | $5,000 - $12,000 |
Electrical Package | $2,500 - $5,000 | $5,000 - $15,000 |
Insulation | $1,500 - $3,000 | $3,000 - $7,000 |
Interior Finishing (Basic) | $5,000 - $10,000 | $10,000 - $25,000 |
Beyond these specific modifications, several factors influence overall project costs:
Cost-Increasing Factors
- Custom design elements
- Premium materials and finishes
- Complex structural changes
- Remote location logistics
- Expedited timeline requirements
- Special permitting or engineering
Cost-Saving Strategies
- Standard modification packages
- Phased project approach
- Simplified interior layouts
- Flexible timeline planning
- Selecting appropriate container grades
- Minimizing custom fabrication
For budget-conscious projects, container rental options with modifications can provide flexibility while reducing upfront investment costs.
Real-World Applications and Case Studies
Examining successful container modification projects provides valuable insights into practical applications and innovative solutions. These case studies showcase the versatility of container architecture.
Case Study: Mobile Construction Site Office
A national construction firm needed relocatable office spaces that could be easily transported between job sites:
- Challenge: Traditional office trailers required specialized transport and were prone to damage
- Solution: 40ft high cube containers modified with offices, meeting spaces, and restrooms
- Features: Solar power integration, satellite communications, custom branding
- Result: 40% reduction in setup/breakdown time between project relocations
- ROI: Projected 3-year payback through reduced mobilization costs
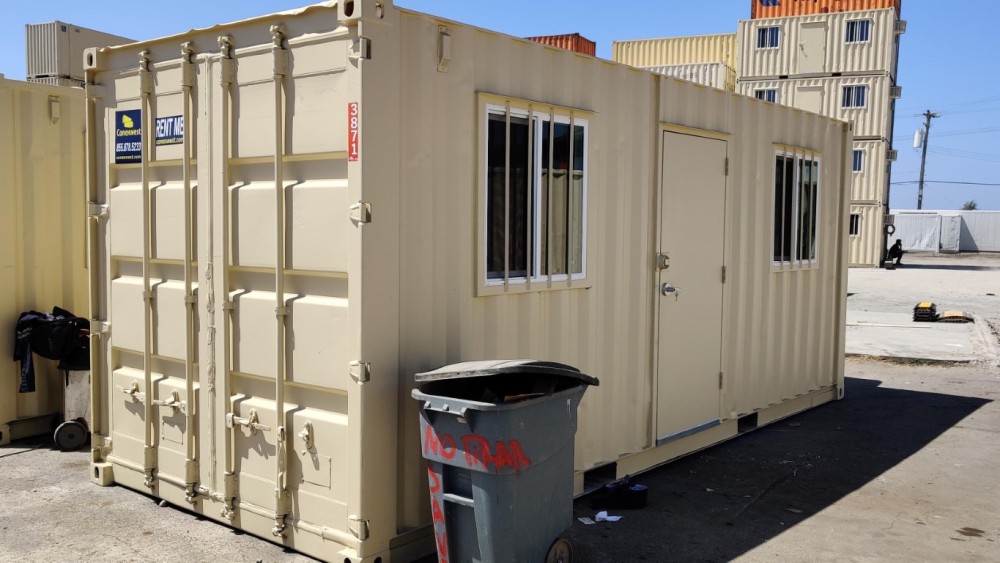
Container modifications provide approximately 30% faster deployment and 25% greater mobility compared to alternative modular construction methods, creating significant operational advantages for businesses with changing location needs.
Industrial Applications
A mining operation in a remote location deployed modified containers for:
- Equipment storage with climate control
- On-site laboratory facilities
- Secure tool cribs with inventory management
- Generator and mechanical system housing
- Modular office and communications center
Commercial Applications
A growing retail business utilized container architecture for:
- Pop-up retail locations in high-traffic areas
- Branded customer experience centers
- Seasonal market expansion without permanent leases
- Product demonstration spaces at events
- Secure inventory storage with retail display capabilities
Regulatory Considerations and Compliance
Navigating regulatory requirements is essential for successful container modification projects. Compliance considerations vary by location and intended use but typically include:
Common Regulatory Requirements
- Building permits and inspections
- Zoning restrictions and variances
- Structural engineering certification
- Electrical and plumbing code compliance
- Fire safety and egress requirements
- Accessibility standards (ADA)
- Foundation and anchoring specifications
- Occupancy limitations and classifications
Compliance Strategies
- Early consultation with local authorities
- Engagement of licensed design professionals
- Thorough documentation of modifications
- Third-party inspections and certifications
- Compliance with international building codes
- Regular updates to meet changing requirements
- Industry standard certifications
- Professional installation documentation
Working with experienced container modification specialists helps navigate these regulatory complexities, ensuring your project meets all applicable requirements.
Maintenance and Longevity
Properly maintained container structures can last for decades. Understanding maintenance requirements ensures your investment retains its value and functionality over time.
With appropriate maintenance, modified shipping containers can maintain structural integrity for 25+ years, offering exceptional long-term value compared to many traditional temporary structures.
Preventative Maintenance Schedule
- Quarterly inspection of seals and weatherproofing
- Semi-annual check of structural elements
- Annual inspection of roof and drainage systems
- Biennial reapplication of protective coatings
- HVAC system servicing as recommended
- Electrical system safety inspections
Long-Term Preservation
- Corrosion prevention treatments
- UV-protective coatings for exterior
- Proper foundation to prevent moisture issues
- Ventilation maintenance to prevent condensation
- Structural assessment after extreme weather
- Regular updates to systems and finishes
For businesses operating container offices or facilities, developing a formal maintenance program helps protect your investment and ensures uninterrupted operations.
Frequently Asked Questions
- What types of shipping containers are best for modifications?
One-trip (new) containers are ideal for most modifications, especially for habitable spaces, due to their pristine condition and lack of chemical contamination from previous cargo. High cube containers (with an extra foot of height) are popular for offices and living spaces. For specialized projects, open-top containers or flat racks may offer advantages. The optimal container depends on your specific project requirements, budget, and intended use.
- How much do shipping container modifications typically cost?
Basic modifications start around $5,000-$10,000 for simple door and window additions. Mid-range modifications including electrical, HVAC, and basic interior finishing typically range from $15,000-$30,000. Comprehensive custom builds with premium features can range from $30,000-$100,000+. Many factors influence cost including container size, modification complexity, materials quality, location logistics, and regulatory requirements. Working with experienced modification specialists provides the most accurate cost projections.
- Do modified containers require special foundations?
Yes, most permanent container installations require appropriate foundations. The specific foundation depends on soil conditions, local building codes, and the container's intended use. Options include concrete piers, slab foundations, footings at corner castings, or gravel beds with proper drainage for temporary installations. Containers should generally be elevated slightly above ground level to prevent moisture problems and allow for proper inspection and maintenance of the underside.
- How long does a typical container modification project take?
Basic modifications can be completed in 2-4 weeks after approval. More complex projects typically require 6-12 weeks from design approval to completion. Custom, multi-container projects may take 3-6 months. Timeline variables include modification complexity, permitting requirements, material availability, and current production schedules. Working with established modification specialists who have streamlined processes can significantly reduce project timelines.
- Can shipping containers be modified for extreme climates?
Yes, containers can be modified for extreme environments with proper planning. For hot climates, modifications include high-performance insulation, reflective roof coatings, shade structures, enhanced ventilation, and high-efficiency HVAC systems. For cold climates, container modifications focus on superior insulation (often spray foam), vapor barriers, condensation management, cold-rated utilities, and supplemental heating systems. The steel structure itself is inherently durable in most climates when properly prepared and maintained.
- Are container modifications code-compliant for commercial use?
Container modifications can be designed to meet commercial building codes, but compliance varies by jurisdiction. Professional container modification companies work with structural engineers and permit specialists to ensure designs meet applicable international building codes (IBC), local amendments, and specific occupancy requirements. Key compliance areas include structural integrity, egress requirements, fire protection, accessibility standards, electrical systems, and occupancy regulations. Early consultation with local building officials is recommended for commercial projects.
- Can containers be combined to create larger spaces?
Yes, containers can be combined both horizontally and vertically to create larger, more complex structures. This typically involves removing portions of the container walls and installing appropriate structural reinforcement to maintain integrity. Combining containers requires careful engineering to address load distribution, connection points, and waterproofing at the joints. Professional modification specialists can create custom structural plans that safely maximize usable space while maintaining the inherent strengths of container construction.
- What is the environmental impact of container modifications?
Container modifications generally have positive environmental impacts compared to traditional construction. Benefits include repurposing existing materials (approximately 3,500kg of steel per 20ft container), reduced construction waste (up to 40% less than traditional methods), minimal site disruption, and lower embodied energy. Additionally, the inherent modularity allows for future disassembly and reuse. For maximum sustainability, consider energy-efficient systems, sustainable interior materials, and renewable energy integration in your container project.